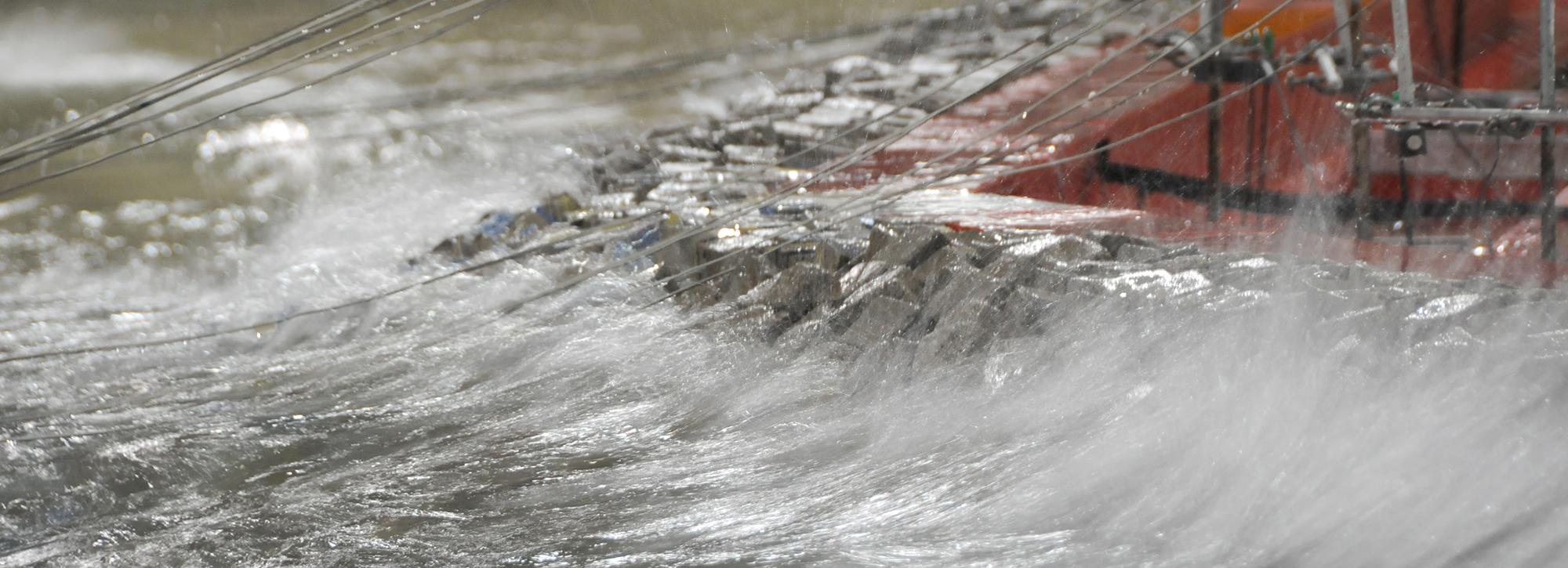
The future is bright for physical modelling
Predictions of the downfall of physical modelling due to improvements in computer power have been made for several decades, and yet our extensive modelling laboratories continue to operate at, or near to, full capacity. Dr David Todd explains why physical modelling of coastal and offshore structures is still relevant and necessary.
Over the last 70 years, we have constructed scaled models for everything from breakwaters to beaches, turbines to tsunamis, and pumping stations to fish passes. Our modelling facilities are the largest and most versatile in Europe, with over 14,000 m2 of laboratory facilities including eight basins, five flumes and abundant space for custom-built, stand-alone models.
We have averaged 28 modelling projects per year over the last 10 years, with durations ranging from several weeks to many months, and projects often occupying more than one facility. What's more, three of our largest ever models have been constructed in the last two years alone. So why is physical modelling at HR Wallingford so enduringly popular despite the predictions of its downfall?
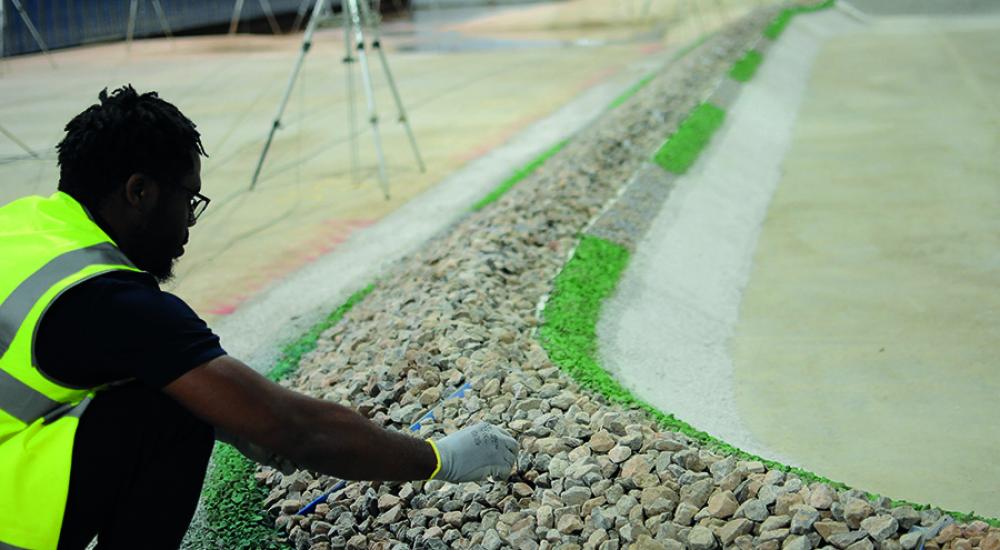
It's a matter of complexity
Physical modelling occupies a space between two forms of numerical computer models that are used to simulate small geographical areas, and really large areas. Between them, there is a size and type of simulation – for example for breakwater stability across full port or harbour areas, or erosion and accretion of beach areas – where it is still more cost-effective and efficient to use physical models.
For large geographical areas – of the order of tens to thousands of kilometres – “large area” models, such as the TELEMAC suite, are used. These models have a resolution (the distance between points at which calculations are performed) of metres to kilometres, and are used for simulating, for example, the sediment transport along a large area of coastline, or the wave climate approaching a port.
These models are extremely useful for providing approximate results across a large area, but lack the fine resolution often required for structural design studies. Due to their size, these models must necessarily contain simplifying assumptions or equations for the models to run efficiently. This, coupled with the resolution of the model, often makes them less suitable to look at the interactions between, for example, waves and a breakwater, as the model is not sufficiently refined to allow the motion of individual rocks or armour units to be estimated.
For very detailed studies of small areas, CFD (Computational Fluid Dynamics) models such as OpenFOAM are used. They are ideal for small geographical areas – of the order of centimetres to metres, such as the end of a breakwater or a power station outflow. The resolution of CFD models is much greater than that of the “large area” models.
However, due to their complexity, CFD models are computationally expensive, and therefore not as well suited as physical models to simulating complex areas, such as scour protection around bridge piers or offshore wind turbines, in terms of cost and effectiveness.
Physical modelling also has several advantages over computational techniques:
- Physical modelling requires few simplifying assumptions, with no requirement to, for example, select a turbulence closure scheme or bed roughness formula, as nature takes it course;
- Immediate visual feedback is provided. There is no need to wait for a model run to complete to view results if damage occurs part way through a test;
- Uncertainties are reduced, as models are less reliant on empirical formulae which may need to be verified or extrapolated outside of their experimental range;
- Users have a high degree of control over the experiments. They are able to make quick changes between, or even during, tests to maximise benefits;
- These combined factors provide surety – clients can believe the results they obtain.
Scaling the problem
Over time, as computer power improves and computer code becomes more efficient, it is likely that computer modelling, and in particular CFD modelling, will begin to impinge on the area in which physical models are traditionally used. At HR Wallingford, we regularly use CFD modelling in parallel with physical modelling for models such as power station intakes and outfalls, dropshaft simulations, and 2D flume studies of overtopping, transmission and forces. However, the advantages of physical modelling are such that it will be decades, rather than years, before CFD competes on an even keel with 2D flume armour studies or 3D large basin studies.
At the same time as CFD is gaining in popularity at the smaller end of the physical modelling scale, physical modelling is expanding at the larger end. Clients are requesting larger physical models simulating larger coastal areas and bigger port developments. At this end of the scale, physical modelling is breaking new ground, with HR Wallingford unique in our ability to combine facilities to create very large basins (up to 75 m x 32 m), offering excellent project scales that reduce scale effects and improve confidence in model results.
Scaling of the models is a crucial consideration, and we use different scaling mechanisms for different purposes within physical models. Models may be scaled in different ways to focus on different areas of interests, including armour or core stability, permeability, sediment transport, turbulence etc. As with all forms of modelling, the results and output of a physical model depend upon the quality of the input data, knowledge and expertise. To provide the right inputs, and select the correct scaling methodology, it is important to understand the purpose of the model – the effect or phenomena that the client requires information on.
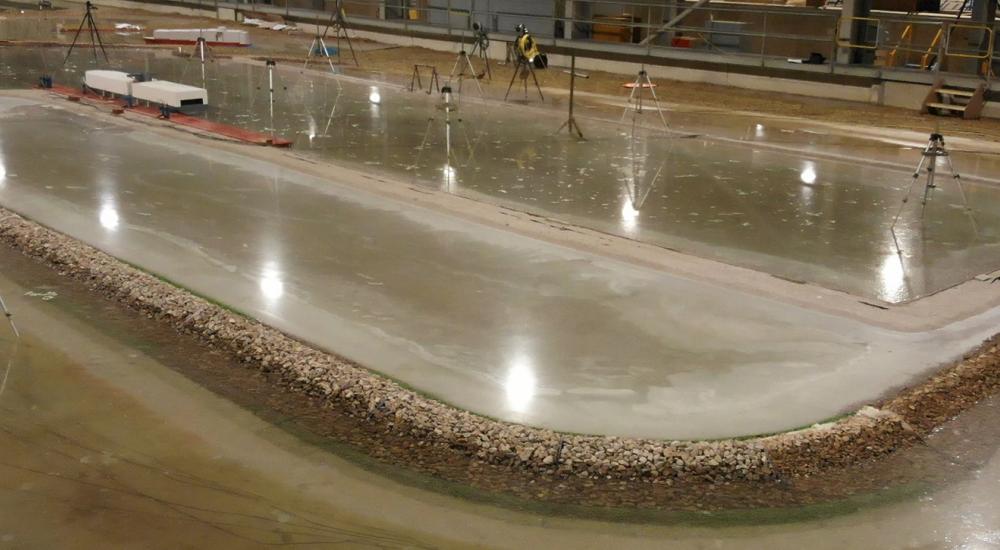
The best tool for the job
Area, CFD and physical modelling are all used to help our clients reduce the risks associated with their business. While a client could, for example, choose to construct a port anywhere, these expensive developments come with inherent risks – the dredged channel may fill in, the quay may overtop, the waves may be too high to allow the ships to load, unload or disembark. With 70 years’ experience, a suite of world-class modelling facilities, and a hard-earned reputation as the global experts in the field, we are ideally placed to select the best, and most efficient, tool for the job.
That best tool is often physical modelling, and that won’t be changing any time soon.