Designing marine facilities for hydrogen: a risky business?
In theory hydrogen is on course to help meet global net-zero targets, but in practice transporting and storing hydrogen comes with significant risks.
Can the port sector’s existing expertise and safety culture, along with planning tools, rise to the challenge of designing marine facilities for a hydrogen economy? Iain Gunn, sector lead for energy at HR Wallingford, investigates.
Why is hydrogen important?
In the race to NetZero, most major economies are rapidly elevating green hydrogen in their energy strategies. Recent research published in the International Journal of Hydrogen Energy suggests that by 2050, hydrogen could account for over 10% of the global energy consumption mix, from a near standing start today.
This is because hydrogen serves as a bulk storage medium for energy from intermittent renewable sources such as wind and solar technologies, and can support the decarbonisation of energy intensive sectors such as the steel and cement industries. The renewable energy that is stored and carried by hydrogen is released cleanly, and relatively easily, as heat through combustion, or as electricity using fuel cells.
How can hydrogen be transported?
Essential to building the hydrogen economy will be transporting hydrogen at low cost. Shipping will connect green hydrogen production, which will be near cheap renewable power, to where the it will eventually be used.
Over short distances, pipelines are likely to be the most cost-effective way of transporting hydrogen in bulk. However, for longer distances, hydrogen will have to be moved by sea as liquid hydrogen, or as a liquid chemical carrier such as organic hydrogen, methanol or ammonia. So, ports and shipping have a critical role in enabling the hydrogen economy by upgrading their infrastructure and technology.
A key question for the maritime industry is the form that hydrogen is transported in. This is partly determined by economics, because the costs of transporting hydrogen (and its derivatives) are balanced between factors such as: the type of renewable energy used to produce hydrogen; transport distance; the cost of electricity for the packing and unpacking of the hydrogen product; and the end user requirements.
At present it seems most likely that hydrogen will be transported as a liquid hydrogen or ammonia. Both have their advantages and disadvantages, but both are more complex than transporting the fuels of today, such as LNG.
Liquid hydrogen is supercooled at atmospheric pressure to -237°C to turn it into a liquid, so it requires pressurised transport and is difficult to contain due to the small size of hydrogen molecules. It is also explosive on ignition.
Transporting hydrogen as liquid ammonia (NH3) may be a better option because it can be stored at the warmer temperature of -33°C, and produced using a simple chemical reaction. This means it needs a lot less cooling than liquid hydrogen, but the downside is that ammonia is extremely toxic.
The table below shows how hydrogen and ammonia compare to LNG, which is probably the closest comparison we have at the moment for bulk transportation of energy by ship.
Natural gas (Liquefied natural gas (LNG)) |
Hydrogen | Ammonia | |
---|---|---|---|
Energy density (as liquid) | 22.2 MJ/L | 10.0 MJ/L | 12.7 MJ/L |
Liquid at (at atmospheric pressure) |
-162°C | -253°C | -33°C |
Stability | Burns back if unconstrained, less dense than air |
Explosive, much less dense than air |
Less easy to ignite, less dense than air |
Transport | Non-pressurised | Pressurised | Semi-pressurised |
Toxicity | Non-toxic | Non-toxic | Highly toxic |
Largest liquid carrier (2023) | circa 260,000 m3 | circa 1,250 m3 | circa 93,000 m3 |
Practical portside considerations
So, in simple terms, transporting liquid hydrogen requires extreme cooling and can be explosive, but ammonia is extremely toxic, meaning both are difficult to design for. But we are facing a climate emergency, so it’s crucial we resolve these challenges and work towards making a hydrogen economy a reality.
While practical experience with hydrogen and ammonia is still building, there is a lot of uncertainty about transporting these products in bulk. In most cases, this is not helped by an absence of port-specific standards or guidance for the transportation of these fuels as a product. That said, the guidance on using alternative fuels for ships is now developing rapidly.
Ultimately, the choice of whether to transport hydrogen as liquid hydrogen or ammonia will determine the import and export facilities required in terminals. But, whichever option prevails, ports will need to adapt infrastructure for import and export terminals including: import pipeline vehicle reception facilities; liquefaction and synthesis of the hydrogen product; storage tanks; and marine berths.
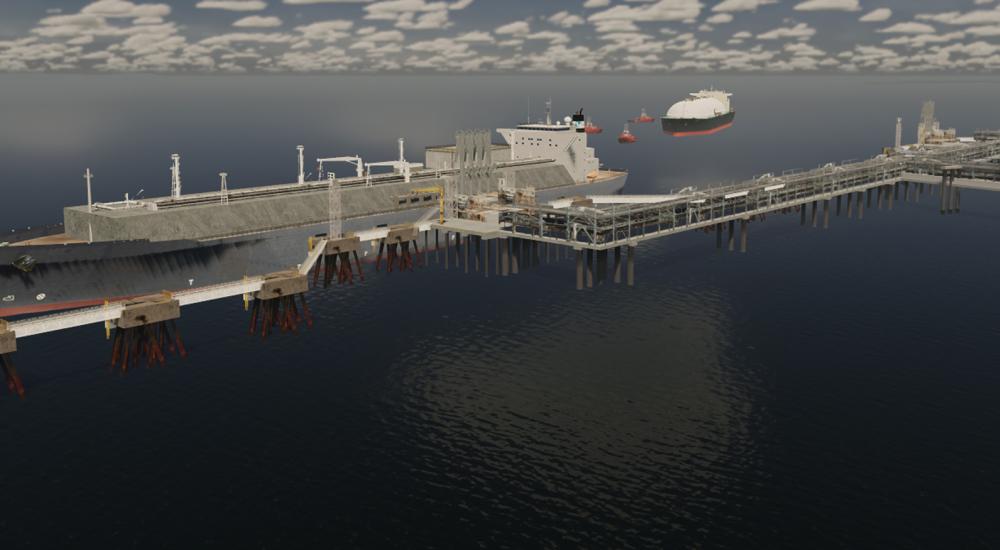
The transition from LNG
We’ve spent decades developing shipping and terminals for LNG, so are there lessons we can learn? Or can we simply adapt the infrastructure we already have?
If we start with shipping, the differing properties of hydrogen and ammonia substantially alter the risk profile associated with marine transportation compared to LNG. This is partly due to the widespread experience of transporting LNG in very large quantities, compared to more limited familiarity with hydrogen or ammonia.
At present, there are only a small number of dedicated ammonia carriers, and one hydrogen bulk carrier on the high seas. These ships are also much smaller than the largest LNG carriers, meaning there is little or no practical experience in planning and managing the port exit and entry for these carriers. However the situation is evolving and the construction of hydrogen and ammonia carriers are in the offing.
When it comes to terminals, it might be thought that existing terminals that are handling LNG have similarities to those needed for hydrogen or ammonia because they receive large bulk liquid carriers with hazardous, cryogenic cargoes. However, the contrasting physical properties of LNG and hydrogen mean that converting existing LNG terminals to hydrogen is a complex challenge requiring new storage tanks, loading lines and loading arms. Because of the cold temperatures needed, the new equipment will also require higher standards of thermal insulation and will use more specialist materials. The lower energy density of hydrogen also means that liquefied hydrogen tanks would store much less energy than an equivalent sized LNG tank.
These practical considerations are similar with regard to liquid ammonia, albeit that equipment associated with ammonia transportation is more readily available in the marketplace. However the toxic nature of ammonia may make retrofitting challenging due to the potentially disastrous impact of spills on nearby facilities or people.
Port planning for a new age
It’s crucial that ports undertake a range of integrated planning studies to achieve the safest and most efficient approach at each terminal.
Two key factors are ensuring that, hugely expensive, land-side storage tanks are the right volume, and that the correct vessel sizes and types can be accommodated in the port. To get the answers, it’s essential to simulate operations of the whole cycle, from export to import. This can be done using software such as the HR Wallingford PortsOps platform.
To get a detailed understanding, the influence of wind and waves needs to be fed into the operations modelling. Both wind and waves have a big effect on the mooring of carrier vessels, so accurate data can help reduce the amount of downtime in the cycle time. The higher the downtime, the more expensive storage systems are required. Likewise the cost of other marine infrastructure including dredged channels, breakwaters and berth position is then balanced with reduced berth downtime and improved cycle times.
Key for new fuels will be a risk-based assessment of the necessary shipping exclusion zones, with consequent knock-on implications for other shipping. During the assessment, it’s also important to confirm that the approaches to and from the proposed terminal are safe by defining weather and safety thresholds for the terminal operations. The best way to achieve this is by conducting a full bridge navigational simulation, including tug requirements.
Risky business or fuel of the future?
It is important to maintain an evidence-based view on transporting hydrogen carriers, and not to over or underestimate the risks.
Indeed, similar concerns have existed for decades for the LNG industry – and this has an excellent safety record. The LNG sector has accomplished over 50 years of marine deliveries without any major loss of cargo. This is based on a safety culture with a strong focus on risk assessment, sound training, well-designed marine port facilities, good governance, and appropriately resourced and planned port operations.
Marine terminals designers, and the people that operate them safely and efficiently, have been outstandingly successful at supporting the vastly increased demand for LNG over the last 50 years. There are few sectors with a better level of safety culture and of transferable skills needed to design, build and operate marine terminals to handle vast quantities of pressurised, cryogenic liquid products. Now is the time for the ports sector to bring these same capabilities to support the energy transition.
Hydrogen-based risks may be different to LNG, but these skills can readily be successfully transferred to other cargoes. Port planning for hydrogen and ammonia certainly brings its challenges – but these are not insurmountable. And it is by dealing with these perceived risks that maritime sector can make an impactful contribution to net zero.
As a sector we start from a good place, with proven, sophisticated tools. These allow us to develop safe and efficient ports of the future and enable the journey to a workable hydrogen economy to become a reality.
Want to know more?
Get in touch
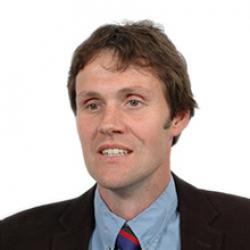